The Cost of a Steel Structure: An In-Depth Guide
3 February 2022. By Joshua Wiggins, General Manager
What Affects the Price of a Steel Structure?
IN BRIEF
- Factors that drive building costs up include adding insulation, roller shutters, custom components, special property requirements, larger clear spans, complex engineering for gantry cranes, irregularly shaped buildings or a steep roof pitch.
- Factors that drive costs down include securing a property with fewer overlay or covenant requirements, smaller clear spans, web truss rafters, standard gable roofs, opting for a ZINCALUME® roof instead of COLORBOND®, choosing standard galvanized roller shutters and using cheaper alternative insulations.
- The cost difference between design and construct companies is due to the level of service provided, the raw materials used, their engineering standards, and whether the company is focused on volume or quality.
- If you’re looking for a budget or entry-level structure we probably won’t be a good fit, as we aren’t the cheapest in the market. However – if you’re looking for a personalised, consultative approach and a high-quality custom design that will suit your needs for decades to come, we’d be happy to help.
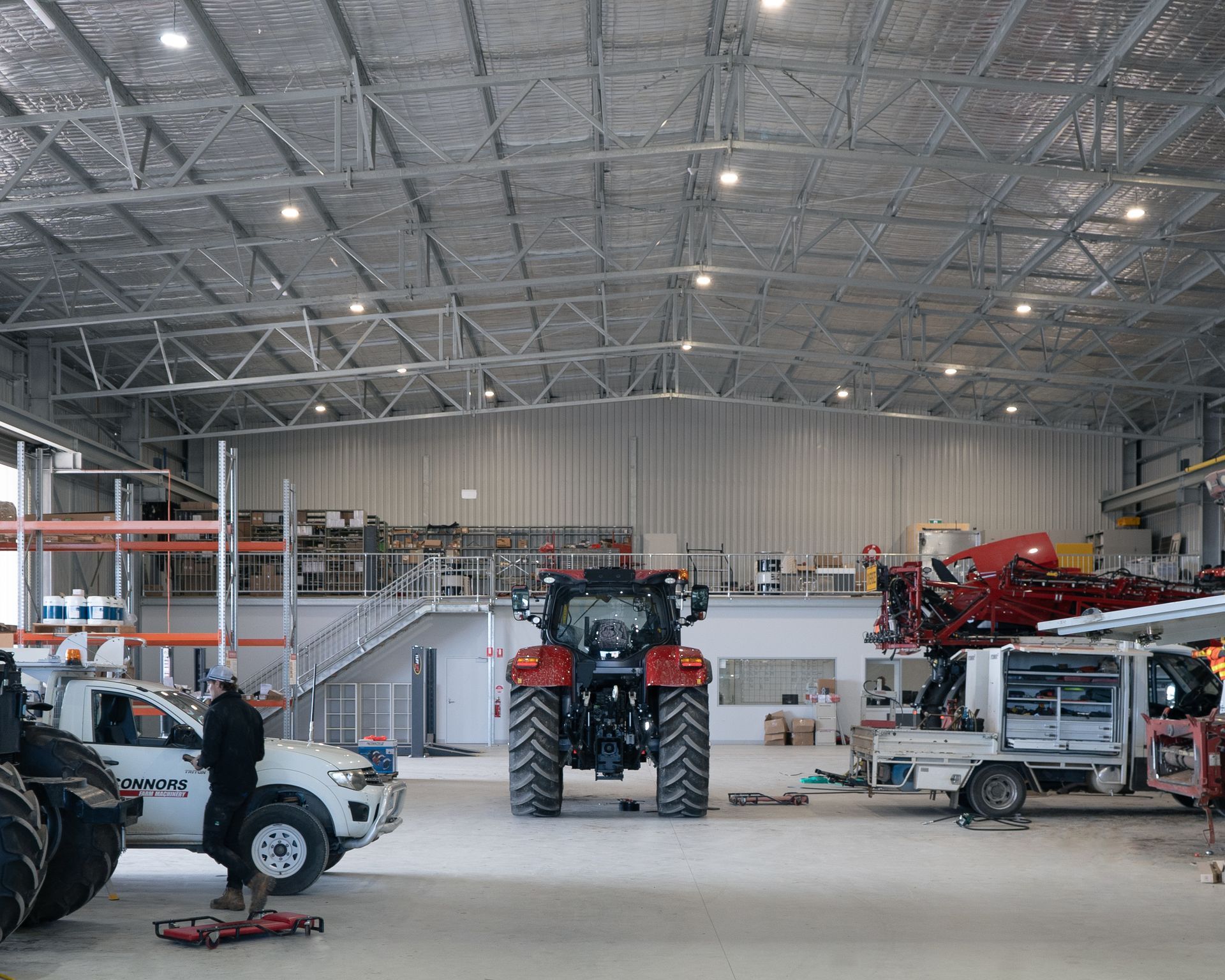
An Unbiased Look at Commercial Building Costs
Planning an industrial building or warehouse project often comes with a range of proposals that differ significantly in price. But why such variation? On the surface, the proposals may seem comparable: same size, similar materials. However, beneath these similarities lie dozens of factors, from roof shape to the level of support provided by your industrial steel builders.
In this article, we’ll explore the key drivers of industrial shed costs and offer tips to ensure your steel structure meets your needs without breaking the bank.
Factors That Affect Industrial Shed Prices
There’s a good reason that some steel structures come with a higher price tag – but that doesn’t mean you have to pay through the nose for your project.
You’re in control and you know what your budget is, so there’s nothing wrong with prioritising certain features over others or cutting out particular details to save money.
The key however is to work out which features are ‘nice to have’, and which factors are an absolute must. Everyone has different priorities and needs, so this is a very personal decision.

To help you compare steel structure prices with a critical eye, we’ve listed all the different things that can make an impact on the cost of your project.
What Drives the Cost Up?
- Additional Features: Elements like insulation, roller shutters, windows, special facades, awnings, and custom components all increase the price.
- Compliance Requirements: Council-mandated features, such as bushfire overlays or landscaping requirements, add complexity.
- Engineering Complexity:
- Larger clear spans (over 36m)
- Curved roof structures requiring specialised processing and installation
- Gantry cranes demanding robust structural engineering
- Roof and Wall Choices:
- Skillion roofs, steep pitches, or all COLORBOND® cladding can increase material and installation costs.
- Project Classifications: Regulatory requirements vary between building types, such as a Class 10a farm shed versus a Class 8 factory.
- Premium Materials: High-quality insulation, concrete dado walls, and powder-coated roller shutters add to the final price.
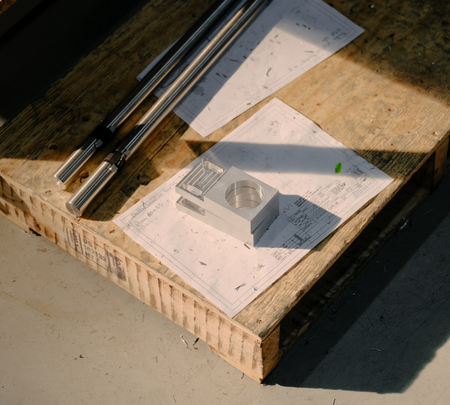
What Drives the Cost Down?
- Streamlining Extras: Skipping roller shutters, special facades, and custom components can save money.
- Site Selection: Choosing a property with minimal overlay or covenant requirements reduces complexity.
- Simpler Designs:
- Smaller clear spans (under 36m)
- Standard gable roofs with moderate pitch
- Economical Materials:
- ZINCALUME® cladding instead of COLORBOND®
- Standard galvanised roller shutters
- Efficient Insulation: Only insulating the roof rather than both roof and walls.
Why Choose Steelcorp for Your Industrial Shed?
Not the Cheapest Option—But the Best Fit for Custom Builds
Steelcorp focuses on delivering high-quality custom steel structures tailored to your needs. We’re not an off-the-shelf supplier and don’t aim to be the cheapest. Instead, we specialise in steel construction services that prioritise:
- Personalized consultation: Ensuring your building meets your exact requirements.
- Premium materials: Using Australian steel and hot-dip galvanised frames.
- Superior engineering: Designing for longevity and compliance.
If you’re seeking a bespoke industrial building solution, Steelcorp’s expertise as a commercial steel supplier ensures your project exceeds expectations.
Where We Operate
We serve clients in Victoria and southern NSW. If you’re based outside this region or need a budget-friendly kit option, we may not be the right fit. However, if you value customisation, quality, and a collaborative process, Steelcorp is here to help.