How to Budget for Building a Warehouse
3 May 2023 By Aaron Barker, Sales Lead
IN BRIEF:
- An average industrial shed costs around $3,000 to $3,500 per square metre for a complete turnkey installation.
- For a structural kit installation only, the cost drops significantly to around $500 to $700 per m².
- The structure itself is just part of your budget: you’ll also need to allow for things like civil works, fencing, soil reports, insurance, office fit-outs, and more.
- You can save money by getting an efficient structural design right off the bat, rather than settling for an inefficient design that has to be re-engineered. Structural design is one of our strengths, so contact us early to ensure you get the right design from the beginning.
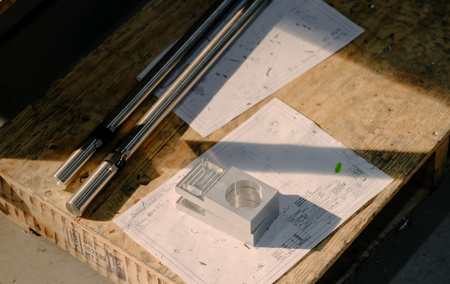
CONTENTS
Average Warehouse Costs and How to Budget for Them
Balancing Costs and Outcomes in Your Warehouse Project
With any warehouse project, accurately forecasting costs and staying within your budget is essential for success. A high-quality industrial building isn’t a win if it results in unmanageable debt or delays other business growth plans. Similarly, cutting corners may save upfront costs but can lead to operational inefficiencies that hamper growth.
Achieving the right balance is about thoughtful planning, starting with accurate budgeting and efficient design.
How to Allocate Funds Efficiently
The best approach for building a commercial steel structure is to dedicate ample time to the research, budgeting, and design phases. These stages take time, but they are critical for ensuring an accurate understanding of the costs involved. If you plan to build in the next year, it’s essential to start the process now.
Aaron, one of our experienced industrial steel builders, advises, “Far too often, we see clients spending excessive amounts on inefficient structural designs. These then require re-engineering, adding time and costs. Structural design is one of our strengths, so contact us early to ensure you get an efficient design from the beginning.”
Factors That Impact Warehouse Costs
Building a warehouse is a large, complex project. Understanding all potential costs upfront helps avoid surprises down the line. Variable costs, such as the price of steel and transport expenses, are particularly important to consider.
Steel prices, for example, are influenced by global market forces and can fluctuate significantly. Similarly, transport costs can vary with fuel prices. Leaving room in your budget for such variables can prevent unwanted surprises and financial strain. Consulting a financial advisor is also recommended to ensure manageable debt levels.
Budget for Building a Warehouse in Australia
Below are key elements to include in your industrial building budget. The specifics will depend on your site, council regulations, and building requirements (e.g., support for a gantry crane). While not exhaustive, this list provides a framework for structuring your project’s costs:
1. Design and Certification
- Fire design
- Structural design
- Civil design
- Soil reports
- Section J (energy reports)
- Council approvals
2. Civil Works
- Hardstand construction
- Drainage considerations
- Driveways and paving
- Signage, bollards, wheel stops, line marking
- Landscaping and curbing (as stipulated by council)
- Perimeter fencing
- Crossovers (connecting your driveway from the boundary to the street)
3. Building Works
- Structural kit and installation costs
- Foundations and slab
- Office and internal fit-out costs (e.g., carpeting, lighting, furniture)
4. Services and Connections
- Water, gas, power, and data connections
5. Fire Services
6. Land Costs
7. Other Potential Associated Costs

- Insurance
- Loan costs and fees for professional advice
- Moving costs (if relocating your operation)
- Tax obligations (e.g., stamp duty, CGT)
- Commissioning of equipment (e.g., HVAC systems)
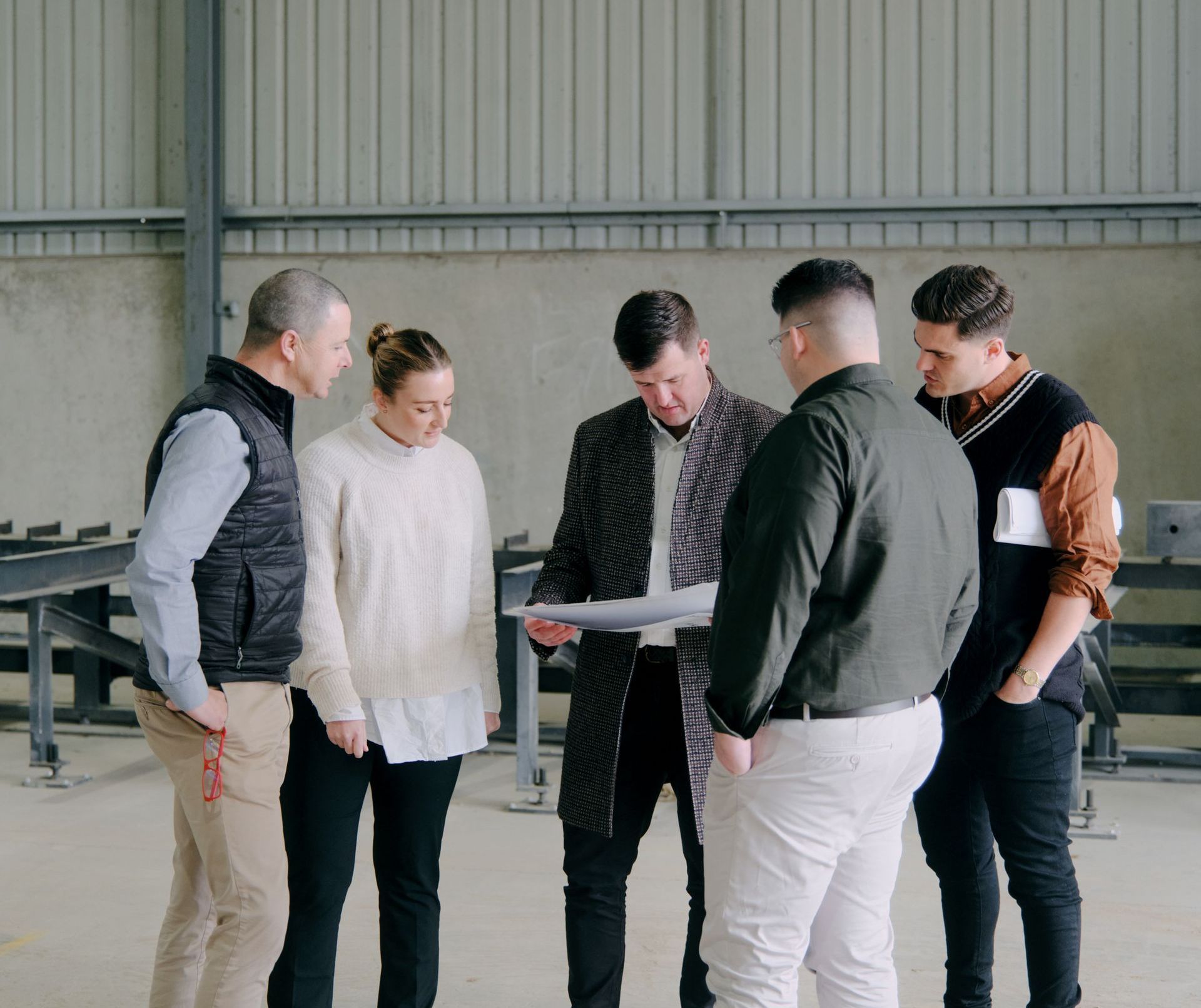
Get Personalised Advice from Steelcorp
At the beginning of this article, we mentioned that the cost per m² for a full turnkey warehouse project is around $3,000 to $3,500. For a structural kit, the cost ranges from $500 to $700 per m². These figures are general guides and can vary based on factors like pavement area, cladding choices, awnings, and other features.
Steelcorp specialises in custom-designed industrial sheds and steel construction services. Our team is here to ensure your project is fit for purpose and delivers a positive ROI for your business.
Ready to start planning your warehouse? Contact us today to discuss your project and take advantage of our expertise in commercial steel supply and efficient structural design.
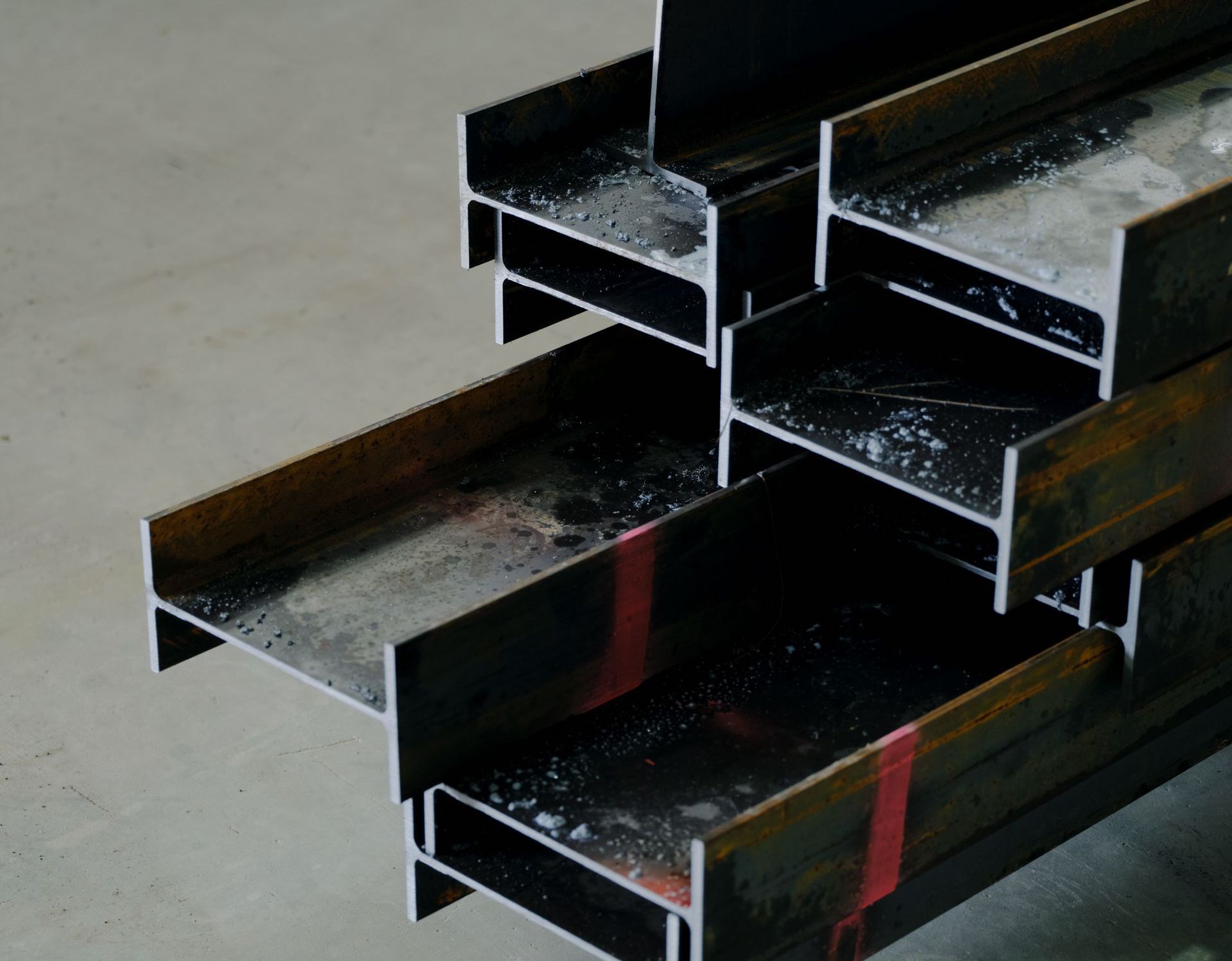
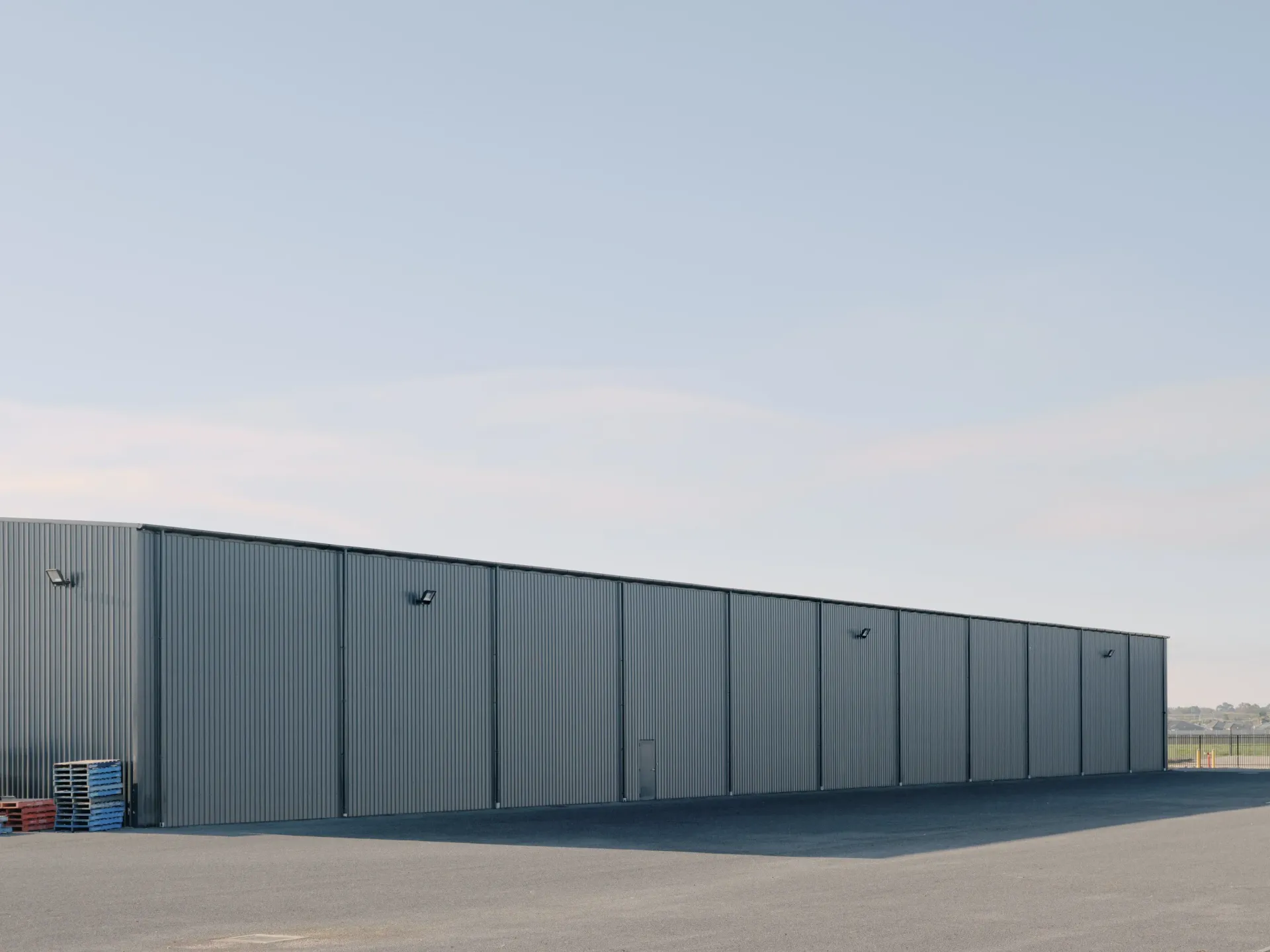